Hello dear modellers! I think everyone has faced the problem of making rails for their projects. Therefore, it was decided to build a circular on the basis of the grinder. The idea is not new, a lot of flocks have already been written on the Internet, well, let me put in my five cents. I warn you that a circular (especially a handmade one) is a dangerous tool! I, as the author of this article, am not responsible for your life and health!!!
To build this unit, we need: 1) Bulgarian (with maximum speed - 10,000 rpm) 2) 125mm disc for wood (with speed - 10,000 rpm) 3) Sheets of metal 4 mm thick. and 2.5 mm. The speed of the disc and grinder must match, because if the speed of the grinder is too high, the disc may scatter, and if it is too low, the cut will not be clean. First, from a sheet of metal 4 mm thick (it is better to take 5 mm), I cut out a “table” 450 mm in size. at 340mm. and cutout for the disk.
Then he tried on the grinder along with the disk. Marked where it will be attached, drilled a hole and screwed it with a bolt. The second fixation point is located on the corner (more on that).
Further from a sheet of metal 2.5 mm. bent the corners. After fitting the entire structure, it was pre-assembled on bolts and nuts. After making sure that the grinder does not hang out, but is well fixed, the bolts and nuts were replaced with rivets.
For the manufacture of rivets, Soviet wood screws were used.
Cutting thickness 2.2 mm. Sawing cleanly, satisfied with the result)
And now a little about the operation of this device. First, the circular is turned on and off using the carrying switch (that is, when assembling, you need to turn on the grinder and DO NOT FORGET ABOUT THIS). Work on it should last no longer than 15-20 minutes, so that the grinder does not overheat. And most importantly, follow safety precautions!
Thank you for your attention. Sincerely, Egor.
P.S. I would like to wish everyone a Happy New Year and wish you good luck, happiness, health and creative success! And may everything be fine in your life!)
www.parkflyer.ru
Do-it-yourself circular: drawings, description and video
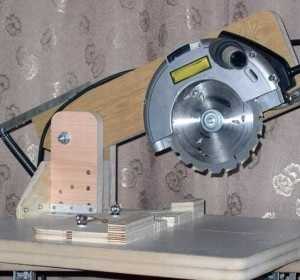
A homemade circular saw is a kind of handy tool that can cope with a number of construction tasks at home. In principle, it will not be difficult to make a circular yourself even if you do not have any special skills, the main thing is to have at least a little idea about working with metal. The necessary material can usually be found in a garage or home workshop, and a steel corner, a rectangular profile pipe and an engine are suitable here. The assembled circular saw can be put on an existing workbench, or, in the absence of such, you will have to build a table for a circular saw with your own hands. As for the motor, you can use the unit from the old washing machine or walk-behind tractor, but first things first.
Hand held angle grinder
If there is a “grinder” on the farm, then there is no better device for a hand-held circular saw. Don't know how to make a mini circular saw at home from such a popular tool? Do not despair, because its manufacture only involves providing a sliding stop and an axial handle to an existing unit. The sliding stop includes in its design two pieces of a metal corner of a small section located on both sides of the saw blade. With the help of bolts and nuts, the corners are connected on the front and back sides with a cross ligament, and the technological gap between the sidewalls of the thrust structure and the working element will be provided with washers.
It is necessary to put on a metal band clamp on the grinder so that its screw tie is located at the bottom, and a strip of galvanized metal with a hole for the sliding stop, folded in half, is already fixed to it. In principle, a special clamp with a stand can be made as a single unit, but in this case, the thickness of the metal strip will ideally be at least one and a half millimeters. Further, in the gearbox housing of the future circular, you will have to make a couple of holes for the bolts, for which it is disassembled, and the drilling points are determined. Through the holes made, an axial handle for a circular saw assembled from a grinder is attached, since the existing handle will not allow high-quality cutting, even if the master has remarkable physical strength.
The axial handle, which will be supplied with a circular grinder, is made of a metal rod or tube. The design in shape can be a transverse bracket or a kind of horn. The ends of the metal part, with which the handle is attached to the gearbox, are provided with holes for fasteners. There is one important point here: the ends cannot be riveted in order to exclude the deflection of the handle during the operation of the hand-assembled circular. It is also necessary to make an adjusting rod from a piece of metal rod (4 - 6 mm), for which we bend one end into a loop, rivet a little and form a hole for the front stop bolt. The uniformity of the gap, as usual, is regulated by washers.
At the other end of the rod, a thread is cut, thanks to which it will connect to the handle. First, one nut is screwed onto the thread, and after assembling the structure, the second one. By tightening and lowering the nuts of this fixture for a homemade hand-held circular saw, the depth of cut is adjusted. This is how at home you can convert the grinder into a full-fledged disk tool designed for cutting various materials. By the way, remaking a circular from a drill, you can achieve a similar result.
Miniature Tabletop Circular Machine
The mobility of the element is achieved by sawing the horizontal segment into two uniform parts, which are fastened with clamps after installation. A circular saw is fixed to the vertical part of the frame on the clamp. A table from a hand-held circular saw assembly can function as a cutting machine if a standard cutting disc is installed on the grinder. It is worth noting that the through cut here will not exceed 80 mm, and for processing larger lumber, a more serious home-made circular machine will be required, which will be discussed later.
Stationary machine
A circular saw, as close as possible to factory models, requires a competent approach to assembly, therefore, before making a stationary type circular saw, you need to think through everything to the smallest detail. In principle, a desktop mini circular saw differs from a stationary one in the height of the frame, which directly depends on the nature of the work performed and the dimensions of the workpieces that the device will process. One-time work can be carried out on a compact table saw, while a circular saw from a hand-held circular saw can be easily hidden in a barn or pantry, and a carpenter who constantly manipulates lumber will need a stationary home-made circular saw. Below is a diagram that details all the elements and fixtures for a circular saw of this type.
As can be seen from the figure, home-made circulars of this type have a clear design, and drawings similar to the one presented above greatly facilitate the process of their assembly. Before you make a circular, as well as mount a circular table with your own hands, we will consider each detail of the unit separately in order to know all the intricacies of its operation and installation.
A table for a manual circular saw with a slot in the center is sometimes remade from an ordinary kitchen table or assembled from bars or metal profiles. Experts strongly recommend covering the table for a circular saw with a sheet of galvanized metal, since without a coating, the base is threatened with abrasion in the center from constant friction of the lumber, which in turn will negatively affect the quality of the cut, and the depth of cut will be uneven. The cross ties that reinforce the saw table are best made from a 60 - 80 mm steel angle with the horizontal segment outward in order to simplify the installation of the side limiter. A home-made table on which a circular saw will be installed must be strong and stable, and it must also be securely fixed in a fixed position.
saw blade
The toothed disc should rise above the surface of the circular table by a maximum of a third of its diameter, otherwise it will not saw the wood properly, and the process itself will become dangerous. If you need to cut a beam with a diameter of, for example, 100 mm, a similar cutter parameter should not exceed 350 mm, however, an engine with a power of 1 kW or more is also required here. For workpieces with a diameter of more than 150 mm, a mini circular made by hand is hardly suitable. On some factory circular machines, a riving knife is provided, which is installed behind the disk at a distance of 2 - 3 mm from the saw teeth. It eliminates the jamming moment due to the closing of the parts of the sawn workpiece, therefore it can be very useful in the case when a home-made circular is assembled.
Side stop adjustable
It is possible to put a high-quality emphasis from a steel corner with a section of about 80 mm, which is 3–4 cm longer than the table structure. The flat sides of the corner are bent down so that their width is one and a half cm more than the thickness of the table. After installation, the stop is fixed on a homemade circular table in a predetermined position with the help of bolts. The adjustment of this element is carried out according to the template placed between it and the cutter.
Shaft
The shaft mounted on the circular is the most critical unit, therefore, only a specialist using special equipment should be engaged in its turning and testing as an assembly with a disk. A pipe product with a carelessly fixed circle is excluded immediately, because the slightest errors in the operation of this element will result in major troubles such as equipment breakdown, damage to the workpiece and injury to the operator. The best solution would be to purchase a finished shaft with a seat for the cutter. It is better to give preference to self-aligning ball bearings that have a curved inner surface, otherwise the assembly made by hand will quickly collapse and the shaft mounted on a home-made circular will become unusable.
Broadcast
In our case, a V-belt drive would be an ideal option, but it is better to refuse a rigid gear mechanism, since such a homemade product does not guarantee safety. If a nail is suddenly caught in the lumber, the motor rotor will provoke the destruction of the disc, which can lead to injury. If the inner diameter of the belt drive pulleys is small, then slippage will be ensured, and the tensioned belt will serve as a kind of damper. The gear ratio is usually chosen based on the engine speed, always taking into account the allowable number of disk revolutions. The smaller the diameter of the saw blade, the greater the frequency of its rotation, and the cleaner the reworked unit will cut.
Motor
Among home-made devices, the most popular is a circular assembled from an engine from a washing machine. This choice is explained by the fact that its operation scheme is best suited for such purposes. Unlike collector units, which are usually supplied with power tools, the engine from the washing machine runs at lower speeds, which means that it shows longer operation, has increased efficiency and is not so prone to all sorts of clogging. You can also use a three-phase motor, but then additional costs will be required for the purchase of a starting and working capacitor, so it is more economical to get by with a device from a washing machine. Here, in general, and all the wisdom. In the video, you can see how a homemade circular works and evaluate its capabilities in practice.
derevo-s.ru
Do-it-yourself circular saw - reliable, practical, cheap!
For any home craftsman, having their own stationary sawing machine is time saving and safe work. You can buy a ready-made stationary circular. The cost of small machines starts from 9,000 rubles, more or less decent stationary saws are sold in the price range from 30 to 100 thousand.
Despite the apparent complexity of the design, any craftsman with elementary locksmith skills can make a homemade circular saw. Moreover, during the design process it is possible to add functions that are not provided by the manufacturer.
What is a circular saw for?
Before starting work, it is necessary to determine the main tasks of the sawing machine. If you just need to cut firewood for the winter, or do basic carpentry work like making a fence, a sturdy table with a slot for a saw blade is enough. Such options are popular in rural areas.
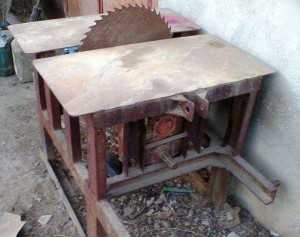
Of course, there can be no question of any safety and functionality when using such a device.
In some of these "models" there is a shaft for fixing the knives of a planer or jointer. As a rule, a bed is cooked from a corner or a channel, an electric motor is fixed on it from a decommissioned factory ventilation, and with the help of a pulley, the torque is transmitted to the disk. It makes no sense to describe in detail the manufacturing technology of such a machine.
Another thing is if you want to do carpentry work. In this case, you need a coordinate table with guides that are fixed at different angles. Since such a stationary saw can work with small workpieces, it is necessary to take care of the safety of the operator. It is desirable to provide for the adjustment of the rotation speed and the possibility of easy change of discs with different diameters.

Be sure to install a protective cover over the disk, and cover the rotating parts of the drive with covers. The starting device is equipped with an emergency switch, and the stop button is placed in an accessible place and is made large.
Don't miss in an accident
How to make a circular, keeping a balance between economy, functionality and safety
Bed. The frame can be made from a metal corner (channel) purchased from scrap metal collectors. If you have the funds, contact the metal rolling warehouse. Legs can be made from old water pipes, connecting them with corners.
IMPORTANT! The use of bolted connections is prohibited, because due to vibration, such a mount will unwind.
Electricity must be used. Be sure to reinforce the corner joints with a jib. The upper part of the frame (on which the table will rest) and the podium for the electric motor are made from a corner with a side of at least 50 mm. If the machine is equipped with wheels for movement, they must be with steel rims and have locks. The higher the mass of the bed, the more stable the machine will be, and the safer the work will be.
Table. The working surface is made of steel, duralumin or silumin sheet. It is permissible to use textolite, plexiglass or moisture-resistant plywood. Galvanized sheet is stuffed over plywood. The main condition is that the material should not crack from vibrations, have a smooth surface and prevent deflection under a weight of at least 50 kg. If the countertop cracks or warps, the circular disc will jam.
This will lead to injury and damage to the workpiece. The use of popular OSB and chipboard materials is undesirable. These materials are unstable to vibrations, and can collapse at the most crucial moment.
There are two options for making a working groove for a circular disc. You can cut a groove or place the two halves of the countertop at a distance from each other. The disc should protrude above the table by no more than 1/3 of the diameter.
For any work, from sawing firewood to carpentry, a reliable side stop is needed. It can be a metal corner or a solid wood bar. To adjust the working gap, you can provide parallel grooves on the tabletop or simply fix the stop with clamps.
IMPORTANT! The side stop must be parallel to the plane of the disk. The slightest deviation will lead to jamming.
Engine. It is impossible to install the electric motor "by eye". Power needs to be calculated. For a disc with a diameter of 350 mm, a 1 kW motor is required, for a diameter of 170 mm, 500 W is enough. A good option is a motor from an old washing machine.
It is designed for continuous operation with medium load. If you plan to work with a disc larger than 350 mm, you can use a power plant from used industrial ventilation. Large electric motors, as a rule, are mounted on dampers (shock absorbers) that prevent unnecessary vibrations.
For a stationary saw, this is unacceptable, since a belt or gear drive will not provide constant engagement. Therefore, the engine is fixed on a rigid and solid foundation. To adjust the tension of the belt pulley, it is possible to move the motor.
Drive unit. The best option is a V-belt. You can use a V-ribbed drive belt complete with pulleys from a car engine. The belt drive guarantees a certain safety in the event of a jammed disc (for example, a nail in the workpiece). Unlike a rigid gear train, the belt will slip on the pulley, preventing the circular disc from breaking.
If the electric motor does not have a speed controller, you can make interchangeable pulleys of different diameters. This will make it possible to use discs of all types, for various working speeds.
Shaft. Perhaps the most important part of a homemade circular saw. It is unsafe to engage in handicraft production from a piece of pipe, so it is better to order it from a good turner or buy it ready-made. The same goes for mounting bearings. To save money, you can use hub kits from the car.
Bearings must be protected from dust; for this, a gasket casing is installed in the grooves between the bearing races. The shaft may have slots with attachments for planer knives. In this case, it must be balanced. It can also be equipped with cutter mounts. Then the machine will be able to produce paneled doors and cornices of complex shape.
Electrical part. The starting device must match the power of the electric motor. The safest option is push-button, with thermal protection for overcurrent. In this case, when the disc is jammed, automatic shutdown is possible. The switchboard is mounted on a dielectric material, the wiring is reliably isolated from the metal frame. The shutdown button is located in an accessible place, it should be pressed without effort.
Often these machines are stored on the street. Therefore, the electrical part must be protected from direct moisture. When designing a homemade circular saw, it is necessary to provide for the possibility of its repair, maintenance, replacement of worn parts.
Moving parts must be lubricated. Before practical work, drawings are made, which provide for any little thing. Any manufacturing error entails the purchase of a new material, which will inevitably increase the cost of the structure.
Circular saw from grinder or circular saw
If there is no need to work with massive wooden blanks, you can make a small-sized stationary saw from a finished power tool. Circular Saw. Ready and fairly safe tool. There are two options for stationary use.
You can simply fasten the saw to the bottom of the table so that the blade protrudes above the surface to the required height. The difficulty is that the switch will be inaccessible. Therefore, it is necessary to block it and duplicate the starting device or remove the standard switch from the body of the circular saw. This is effective but not safe.
How to use a circular saw as a circular saw you can see in this video
Another option is a sliding bed. The base is mounted from two parallel metal guides. A frame with rollers and a fixed circular saw is installed on it. The workpiece is stationary, and the circular, moving along the guides on the carriage, makes cuts at the desired angle. This easy-to-make machine can actually do wonders for small workpieces.
Manual circular saw on rails
Circular from the "Bulgarian"
This power tool is in the arsenal of any self-respecting master. Instead of a cutting or grinding disc, you can install a toothed saw blade.
Carefully! Sawing a tree with a metal disc, holding an angle grinder in your hands - FORBIDDEN! This could result in serious injury.
"Bulgarian" must be securely attached to the edge of the table, ensuring that the axis is parallel to the tabletop. Only after this is it allowed to mount a steel toothed disk on the angle grinder.
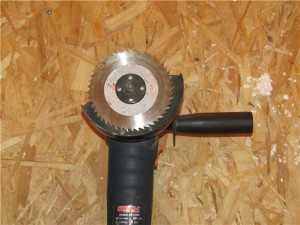
Just as in the case of a circular saw, it is necessary to consider an external starting device. If the "grinder" is equipped with protection against power failure in the network, you will have to make changes to the design of the switch. If the design is simple, it is enough to install a socket with a switch, and fix the start key of the angle grinder in the “ON” position.
All of the above refers to simple ways of processing wooden blanks, that is, "parallel" and "perpendicular". If it is necessary to perform complex carpentry work, the circular requires refinement.
How to make a woodworking machine from a circular saw
Actually the working part (that is, the disk itself) remains in its place. The main element of a full-fledged machine is a moving coordinate table. The best option is to make one half of the tabletop movable so that it moves relative to the rigidly fixed second half and the circular saw.
To do this, in the furniture fittings store, powerful “sleds” for drawers or sliding doors are purchased. The lower part of the slide is attached to the bed, and on the movable upper part, a half of the table is attached. It is important to achieve parallel halves both horizontally and vertically. There should not be any backlash, otherwise the saw will jam.
IMPORTANT! The direction of movement of the sliding table is always parallel to the plane of the saw blade. The required sawing angle is set by the position of the workpiece.
A fixing device for workpieces is installed on the movable tabletop with markings according to the distance from the saw blade and the installation angle. The latch must have maximum freedom to accommodate the workpiece, while at the same time ensuring its secure fastening. You can use clamps.
The workpiece is attached to the movable tabletop at the required angle, the carriage moves, the disc cuts the part at the desired angle. By adjusting the height of the workpiece, you can even cut through grooves. For safety reasons, the fastening of the workpiece must prevent the operator's hands from getting into the working area of the saw.
It is also possible to provide for the deviation of the plane of the circular disk from the vertical. This addition expands the capabilities of the machine and allows you to cut complex configurations. Another option to increase the versatility of a stationary circular saw is a pendulum disc suspension.
Pendulum disc illustration
The engine, drive and disk are mounted on a space frame. One side is hinged on the bottom of the table, the other side is fixed with a screw height adjuster. The disc can rise above the work table to a predetermined height, providing a choice of workpiece thickness. In combination with the rotation speed adjustment, this option makes it possible to install discs of different diameters on one shaft.
Conclusion A homemade circular saw gives you the opportunity not only to save money, but also to add any number of functions you desire. And the use of improvised materials allows you to bring the cost of the device closer to zero.
How to make a stationary circular saw from a manual circular saw is described in detail in the appendix, with drawings and several examples of implementation, which can be downloaded here
obinstrumente.ru
Reliable circular saw from a grinder with your own hands
- How to be and what to do?
- Additional aspects and summing up
When working at home, you often have to resort to such extraordinary solutions as a do-it-yourself circular saw from a grinder. It is not difficult to redo it, but you must immediately remember that this is not safe, and can also lead to very bad consequences.
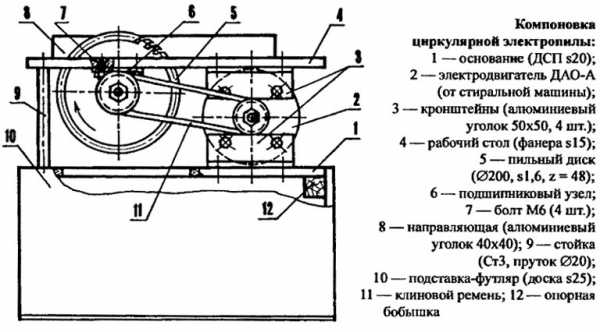
Circular saw design.
How to be and what to do?
Tools and materials:
- drill (screwdriver);
- clamps;
- self-tapping screws;
- bolts with nuts;
- reduction gear.
Regardless of the conversion method, you need to use a low-speed grinder from 4500 to 6000 rpm, because because of the increase in speed, the discs will grind much faster. Along the way, it is worth remembering that the tool that is not a pity is used, because. then you can not restore it back in any case.
In any case, the protective cover is immediately removed, which in the end will be replaced by a simplified counterpart. Then there are several options for the development of events:
Bulgarian device.
- The most benign option. In this case, only clamps and bolts are used for fixing through the countertop. 3 points are fixed with clamps - the main handle, the side handle and the central block is tied up 3 cm from the disk. All clamps are fastened as securely as possible so that there is no free play even by 2 mm, otherwise, during operation, at best, the tool will quickly fail, and at worst, it may fail to break the disc.
- The most expensive among analogues. It will require the support of a turner-miller. He will carve out a fastener that allows you to connect the countertop and the grinder through the block, which until recently served to mount the protective casing. It is this option that is the most reliable, but it is impossible to quickly carry out the process.
- The fastest option. Using long metal screws, fix the grinder at 3 control points. It is important here not to damage anything from the propulsion systems, so that the assembled circular saw with your own hands will work for a start. Self-tapping screws for confidence are used in pairs for each junction.
- Using self-tapping screws, the angle grinder is attached to the gearbox. This method is characterized by a very high speed of work, but also damage to 2 expensive tools at once, therefore it is used only in the most catastrophic cases.
- The previous version is a rare barbarity, but with a little more time, you can achieve better results. With the help of clamps, 3 control points on the grinder are pulled together and bolted to the gearbox. Thus, 2 tools remain intact, but the elapsed time increases up to 10 times.
When mounting to a countertop or any other surface, you need to provide the master with maximum protection, because. discs often break. There is no need to be particularly smart here, because. sheet steel layer perfectly cope with the task. If there is a desire to achieve maximum reliability, then you can use a 3 mm steel profile, which the wood cutter will not break through even at very high speeds. The protective structure is located at a distance of 5 cm from the disk so that the wood passes freely from above.